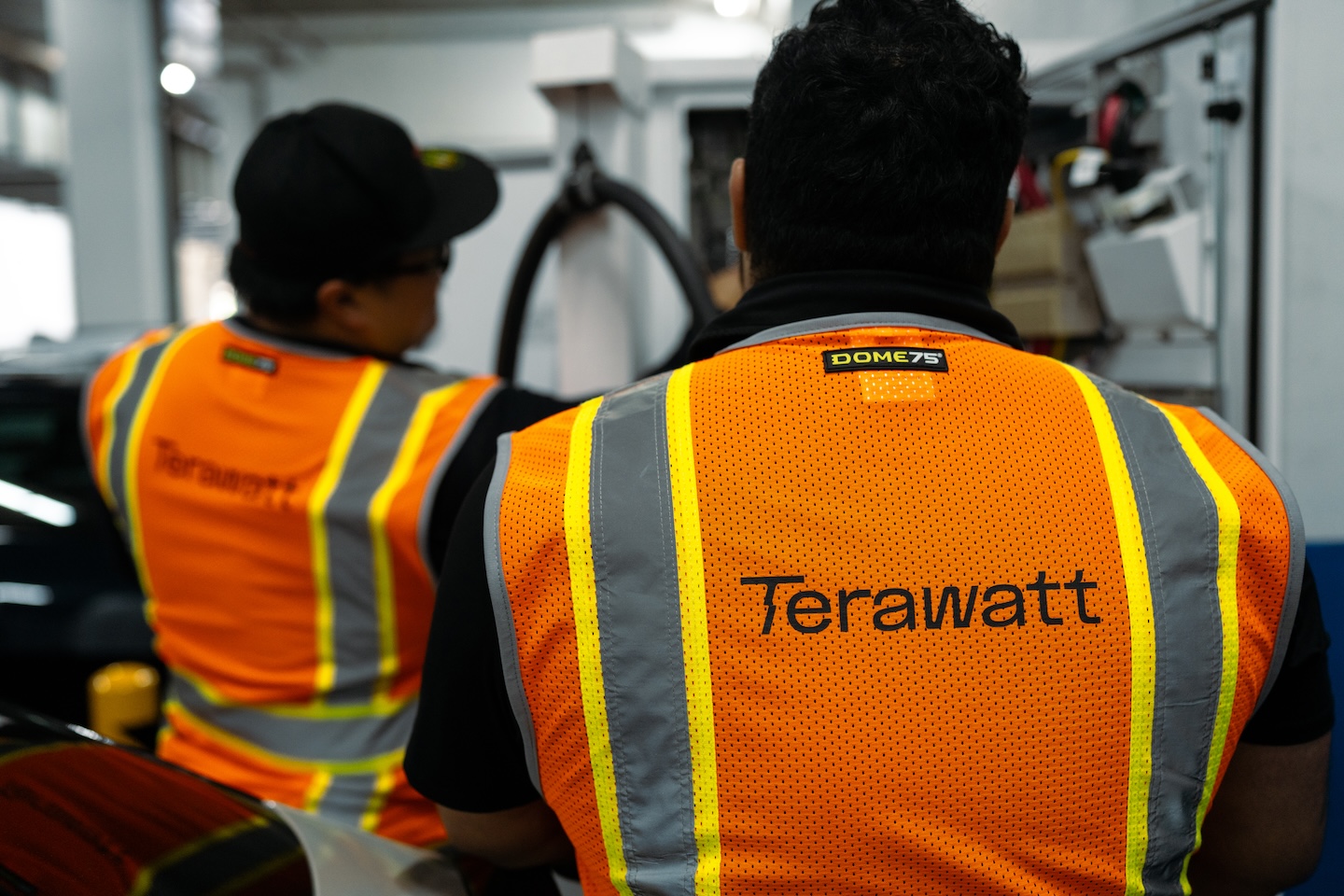
How Terawatt’s Operations Team Fixes EV Chargers Faster Than A Pizza Is Delivered
In case anyone was curious about what a Charging Operations team actually does, let's just say we’re all about getting things fixed at our electric vehicle (EV) charging sites faster than your local pizza place can deliver. Our Network Operations Center (NOC) team works behind the scenes to monitor, diagnose, and resolve technical issues with unmatched speed and precision. Recently, they proved that not only do they know what they’re doing, but they’re setting a new standard for what “fast service” really means. We’re excited to break it down for you below.
How Fast Are We Compared to Industry Standards?
In a public charging network, this type of repair would typically take 3 to 7 days:
- 3 days for the initial inspection
- 4 days to source and wait for parts
In our case, the issue was fixed in 32 minutes.
The Scenario: Charging Stall Goes Down
Last week, we had a scenario where one of the charging stalls at our San Francisco charging site triggered a fault. This was caused by a vehicle requesting more power than the charger could deliver, which tripped the system’s safety mechanisms and temporarily put the charger out of service.
Here’s how we handled it, from alert to full resolution:
- Alert Discovery: At 11:48 a.m., a manual sweep from our NOC team flagged the issue.
- Immediate Action: By 11:52 a.m., we placed cones to mark the stall as temporarily unavailable, alerting customers to the issue before they even noticed.
- Case Generation & Dispatch: Within minutes, a case and work order (WO) were generated. A technician was called, arriving on site by 12:01 p.m.
- Quick Diagnosis & Repair: The technician finished inspecting and repairing the issue by 12:14 p.m.
- Service Resumed: After thorough voltage checks and documentation, the charger was back in service by 12:20 p.m.
Total time to resolution: 32 minutes. To put this in perspective, the customer didn’t even get a chance to report the issue before it was already fixed!
What Happened & How We Fixed It
In this instance, the fault was triggered by a vehicle drawing more power than the charger could provide, causing the breaker to trip mid-session and rendering the charger inoperative. This often happens when an EV is using outdated software or a potentially failing charging component that can cause issues intermittently and eventually spread to a charger failure.
During the process, the peak power request exceeded what the “handshake agreement” was and our charger shut down in the interest of safety. When the breakers were tripped, a warning notification was sent to our Charge Management Software portal where our product and tech team designed warnings for key alerts for critical failures. The alert was triggered during one of our NOC team’s routine hourly sweeps of the Terawatt network for observable conditions and issues that can lead to errors — the moment when we actively examine charger logs and reset them as needed to restore full functionality. The NOC team then immediately generated a work order and dispatched our on-site technician.
Our technician quickly diagnosed the problem by running voltage checks, inspecting key components, and ultimately identifying the issue in the electrical motor operator, which manages power flow. The initial inspection requires a voltage check as any changes in power supplying the machine can change its personality and behavior. During this portion of the inspection our technician traced the break in power to the earlier mentioned breakers. By design, these breakers did their job in fear of a vehicle causing a dangerous charging event. With that said, our tech was able to reprime and reset the breakers easily without any replacement needed. After that, he performed one final voltage inspection from top to bottom to reaffirm that all components were being fed sufficiently and within spec power limits. To finish, he kicked off a charging session with some of Terawatt’s own in-house fleet vehicles to determine the repair was complete, not just adequate.
Our team doesn’t just swap out parts until the problem disappears, as some service providers might do; we follow precise protocols and use our expertise to get things right the first time.
But it doesn’t end there. Even with our fast response, we received a call from the customer three hours later, reporting the issue that had already been resolved. For the customer, this experience went from being a potential hassle to an easy, seamless repair they hardly even noticed.
This feedback reaffirms our commitment to delivering exceptional service, surpassing expectations, and setting a new standard for efficiency in our industry.
Redefining Fast Service for Our Customers
Our Operations team’s goal is simple: identify, diagnose, and repair as quickly as possible, all while ensuring quality and safety. This recent case at our San Francisco garage shows that we’re not only meeting this goal but exceeding industry standards in a way that makes our customers’ lives easier and more efficient.
So, next time you wonder what our Operations team is up to, just remember: we’re fixing issues faster than you can say “extra cheese.”