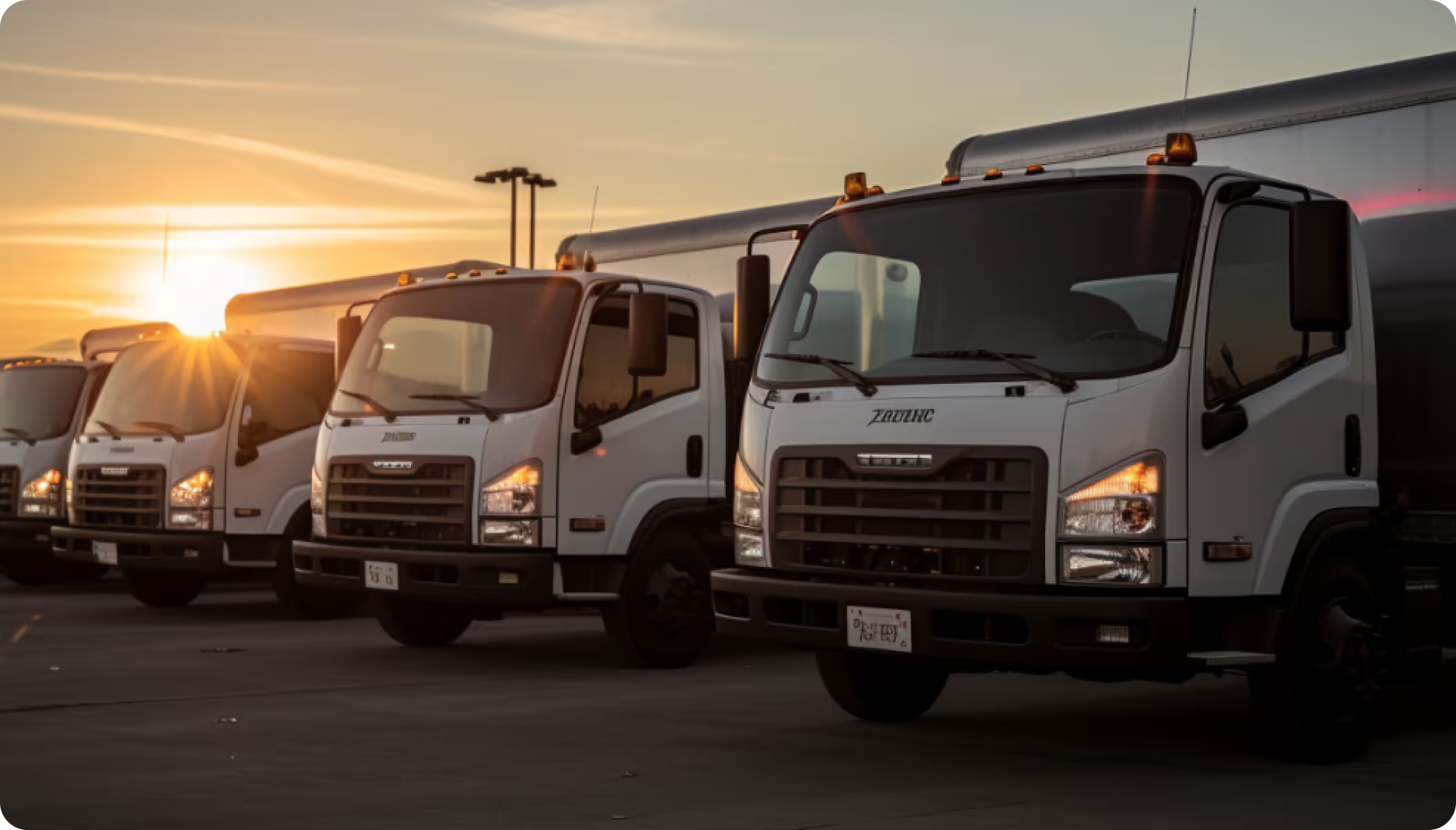
How to Better Predict your EV Fleet’s Total Cost of Ownership
If you’re in the process of electrifying your medium- or heavy-duty fleet, it’s likely that you’re overwhelmed by a sense of uncertainty in the investment. Will your battery electric vehicle (BEV) reach parity with an ICE truck over time? How long will it take to reach that parity? Why are there knowledge gaps that are making it even more difficult to do the math?
While calculating the total cost of ownership (TCO) for traditional diesel-powered trucks is relatively straightforward, the emergence of electric trucks has made it more challenging to estimate the long-term costs. BEVs possess characteristics that are difficult to measure, such as the cost of energy, which varies depending on location and time of day.
The good news: TCO for electric trucks continues to decrease, and studies show that heavy-duty zero-emissions trucks should achieve cost parity with their ICE counterparts quickly. Urban and regional trucks are already cost-superior as of this year, and longer haul is slated to catch up by 2030.
But we know there’s still plenty of confusion out there with respect to specific types of costs, and we’re here to help. Below, we share the TCO research we’ve gathered and we break down all of the various components you’ll need to take into account when thinking about purchasing an electric fleet — and where to go from there.
BEV Total Cost of Ownership Components & Predictions
Total cost of ownership takes into account all the costs associated with owning and operating a vehicle over its lifespan, including purchase price and incentives, cost per mile, fuel, maintenance, repairs, insurance, depreciation, labor, and residual value.
These costs filter into two broad categories: fixed and operational expenses. If fleets plan to build their own charging infrastructure, they can expect significantly higher upfront costs (e.g. vehicle cost and all the required infrastructure costs). If they work instead with an infrastructure partner that’s using its own capex to build charging capacity, those upfront investment costs can be reduced — or even eliminated.
Fixed Costs
Vehicle Purchase Price & Associated Tax
The biggest fixed cost is the vehicle purchase price. As many Class 8 vehicles have just started to come to market, pricing varies by manufacturer, but the International Council on Clean Transportation estimated that the average cost of a BEV in 2022 was ~$450k. Sales of commercial vehicles are also subject to a 12% federal excise tax, therefore resulting in an average total purchase cost of about $500k.
Thankfully, this cost discrepancy should be short-lived, as these purchase prices are expected to decrease steadily in the coming years. According to the ICCT, they should halve as soon as 2030 and reach parity with diesel trucks by 2040. Grants and incentives can also drastically reduce the upfront cost of vehicles when available.
TCO will also improve with greater mileage and more powerful batteries. The larger and more efficient the battery, the longer the vehicle can travel without needing to recharge, further reducing energy costs. Battery right-sizing will also help TCO by decreasing the size of the battery to fit shorter haul use cases, rather than a “one size fits all” BEV design and the limited number of truck models fleets can choose from today.
Operating Costs
Charging Cost
Electricity costs vary significantly by state, depending on tariffs set by the local utility. Common electricity costs can include a volumetric energy charge ($ per kWh), demand charge ($ per kW per month) on capacity, and fixed charges ($/month) for utility service.
Despite these fluctuations, electricity is proven to be comparatively cheaper than diesel (converted to a comparable $/kWh number) in all 50 states.
Infrastructure Cost
In addition to the variable electricity costs, there are various components that go into acquiring, developing, and building the infrastructure required to enable seamless charging. Infrastructure costs include land costs, interconnection to the grid, development costs (permitting, entitlements, surveys depending on the site), construction costs (both electrical and others), and the chargers themselves. Infrastructure costs can vary widely between locations depending on interconnection requirements, labor costs, etc.
Fleets can eliminate this upfront cost entirely by working with an infrastructure partner instead of trying to build it out themselves. Companies like Terawatt have the ability to turn capex into opex by assuming the full cost of the infrastructure buildout — land acquisition; engineering, procurement, and construction; software; site operations and maintenance — and passing it through to the customer, who can pay by the kWh or through a fixed monthly rate.
As more land gets turned into charging infrastructure and battery and charging technology improve, fleets will be able to minimize the amount of infrastructure they need to build themselves — and avoid it entirely in some cases, further decreasing the TCO.
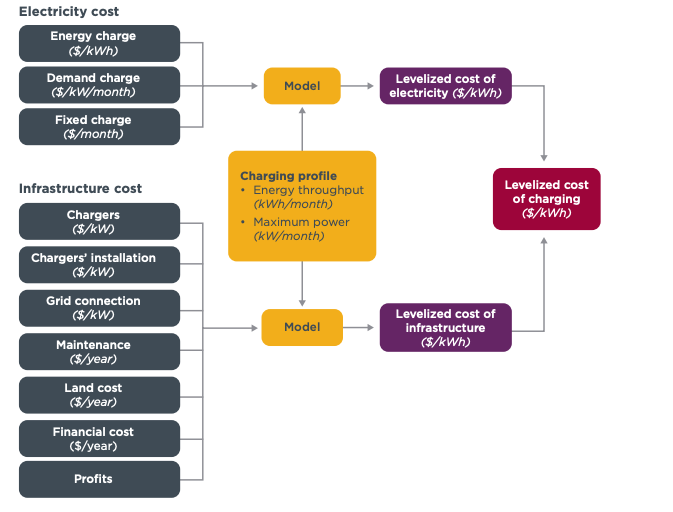
Maintenance Costs
Certain components like brakes, gears, air conditioning, tires, and cabin air filters go into both diesel and BEV trucks — and in both cases, costs will need to be allocated to repair or replace these items over time.
Electric trucks already boast lower maintenance costs than diesel and hydrogen trucks thanks to the fact that they don’t have engines (although some battery-related maintenance costs can be expected). These numbers are expected to decrease further as battery and vehicle technology improve.
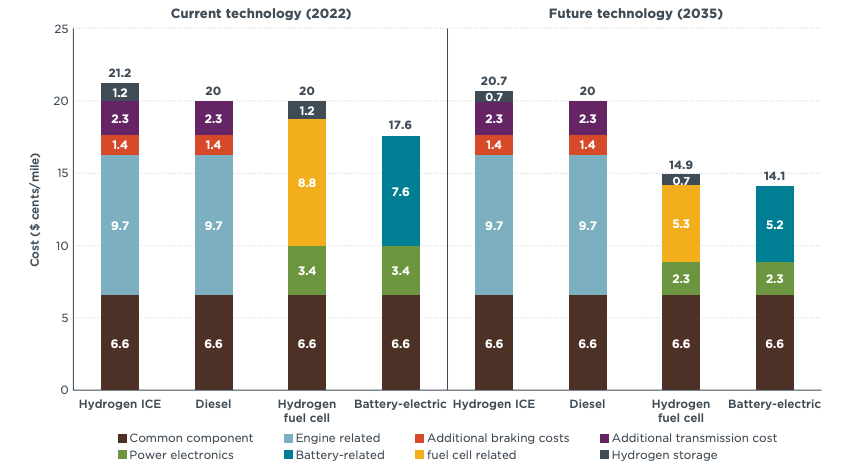
Labor
The big variable on labor costs is the potential need for companies to reconfigure their operations to accommodate charging requirements. Given the currently longer charge times compared to refuel times (until MW chargers are commercially available), BEV trucks may or may not have higher labor costs than ICE trucks, depending on how well the BEV fleet fits into existing operating hours and routes.
Insurance
Given the higher initial purchase price of BEV trucks, insurance costs are also estimated to be higher than traditional ICE vehicles but should come down over time along with MSRPs.
How to Electrify Confidently Despite Total Cost of Ownership Uncertainty
The total cost of ownership of an electric truck remains a highly variable and speculative calculation as of today, making it all the more complicated for fleets to determine their electrification plans. The following list represents the primary factors that contribute to this uncertainty, and some key takeaways that can help to assuage any concerns:
Fuel cost evolution
Electricity costs are actually more predictable than diesel ones, as they depend less on external factors (such as geopolitical conflicts). Instead, they fluctuate based on geographic location and time of day. The exact margin is difficult to predict given the uncertainty in future energy prices, but overall, electricity should remain considerably cheaper than diesel on a dollar per mile calculation.
Infrastructure utilization
If fleets are planning to build their own EV charging infrastructure, it’s important to remember that the more a site is utilized, the cheaper the charging cost, as the infrastructure cost is spread out over more throughput. Working with an infrastructure partner means they’re factoring maximum utilization into their pricing — ultimately keeping your costs as low as possible.
Depreciation & residual value
Electric trucks have only just hit the roads — there are only a few hundred being actively used today. It will take several more years before there’s a concrete sense of how quickly the vehicles depreciate, and what their value on the used vehicle market looks like.
Yet some studies already show that the residual value of an EV truck will equal that of a diesel truck (53% of its original value) after 5 years of operation. The biggest unknown with BEVs is the battery itself, which was estimated in 2022 to have a residual value of 43% after 5 years. If the battery gets swapped out, that residual value increases.
Financial horizon
Fleet owners need to balance the higher upfront purchase price with the incremental cost savings that are expected over a longer time horizon — and this balance may be significantly more favorable in certain geographies or at certain points in time. Purchasing an electric truck in California in 2023, for instance, unlocks a variety of incentives and rebates that can help fleet owners reduce their upfront costs. Several other states are expected to follow in California’s footsteps.
Future freight operations
Given charging time is currently slower than fueling time, this may require fleet operators to tweak their operations, namely by needing to add extra hours, thereby increasing labor costs. Companies can potentially work around this by electrifying smartly — selecting specific lanes and/or use cases that can accommodate EVs without significant operational disruption. Examples include short-haul and drayage, both of which can mix overnight charging with a quick en-route top up.
Next Steps for your EV Fleet
So what does this ultimately mean for you and your fleet? Studies using advanced statistical analysis have shown TCO costs should ultimately favor BEV trucks over diesel as well as hydrogen and hydrogen fuel-cell trucks, making BEVs the most cost-efficient technology over the long-term. The primary advantage to BEVs is they have much lower fuel costs than their diesel counterparts, and technological BEV advances will continue to drive the TCO lower over time.
Ultimately, TCO for any type of vehicle is unique to each fleet. Whether you’re operating diesel or battery-powered trucks, your unique operational conditions dictate the amount you spend on every vehicle you purchase.
The fleet electrification transition won’t be seamless, but the only way to begin penciling out your EV fleet’s TCO is by beginning to integrate those EVs into your fleet. The sooner a fleet embarks on the transition to BEVs, the faster it can begin to take advantage of the long-term economic benefits. Piloting even a small number of EVs today can provide a roadmap for how to scale in a cost effective manner.
You also aren’t alone in this journey. State programs and external infrastructure partners are ready to help you navigate the uncertainty and ultimately de-risk the transition to battery electric trucks.